Frequently Asked Questions
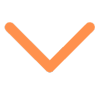
Our technology is based on a dry process, which means we don’t have to use any toxic solvents such as NMP. Furthermore, our technology is binder free, and this means there will be no issues with microplastics and more recyclable.
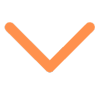
Sienza welcomes any high performing cathode solution and is willing to consider collaboration with any cathode solution provider. Please feel free to contact us if you are interested.
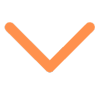
No, there aren’t any unconventional methods.
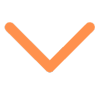
Sienza silicon anode can cycle at 1C.
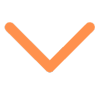
Silicon anodes are widely regarded as the next generation of anode architecture. They have roughly 10x the specific capacity than that of graphite. Sienza strategically chose to focus on the anode first simply because it is the most difficult technical problem. The technical difficulties of silicon-based anodes are not a secret and Sienza believes that we have an answer to the difficulties faced with scaling a silicon anode solution. Additionally, Sienza is concurrently developing in-house cathode using our state-of-the- art 3D architecture. Our overall goal is to merge these two products into one state-of- the-art battery product that will be a competitive solution in the market.
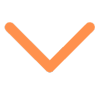
Sienza uses a 3D nanostructure as its morphology. This 3D architecture allows a number of key and unique advantages. The main advantage of this architecture helps with reducing the silicon expansion during charge. Our method of 3D nanostructure dramatically increases the surface area available for active material, thus dramatically increasing our ability to load our substrates with active material. This 3D architecture also allows for dry active material depositing processes. This dry process itself has a number of key benefits as well. A dry process eliminates the use of NMP or other toxic chemicals/solvents that are used in conventional battery manufacturing. This is a paradigm shift in the environmental friendliness of battery technology as well as a dramatic improvement in workplace safety for technicians in the laboratory/production line.
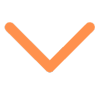
Higher capacity than graphite and silicon is cheap and earth abundant (significant cost reduction due to silicon price).
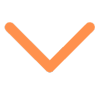
Sienza battery can be used with EV, consumer electronics, power tools, ESS, etc.
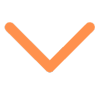
Our battery can be used in multiple applications, with advantages such as: increased energy density, recyclable, and more sustainable.
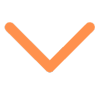
Sienza has a dry production process, no binder, thin silicon coating, and higher cycle life.